FeatureTruly Unstoppable: Armin Strom On Taking The Horological World By Storm With Their ‘Transparent Mechanics’
In the exalted world of haute horlogerie, it’s no mean feat to be able to dig your heels in and stand firm on your ideas and beliefs. Armin Strom are reiterating this with their radical watchmaking approach that comprises a mix of innovation and traditional techniques, enhanced by the impeccable Swiss-German horological standards
May We Recommend
It takes a lot to carve a niche for yourself in the Swiss watchmaking industry, especially when there are brands that boast a rich history that’s imbued with traditional watchmaking know-how and artistic skills. Some of these players are over 150-years-old and have attained a pride of place, whether in terms of being movement specialists, leaders in the chronograph or sports watch segment, masters of decoration or pioneers in complications. Therefore, it becomes even tougher for a young brand to create an identity, more so if you’re an independent. But that’s what Armin Strom have achieved rather successfully in a short span where horologists are now familiar with the watch company offering ‘transparent mechanics’, in the form of exquisitely-crafted timepieces that employ the art of hand-skeletonisation—introduced by founder and watchmaker Armin Strom way back in 1967; long before it became fashionable among the mainstream brands. Today, they are crafting some of the most avant-garde watches bolstered by Swiss-German horological traditions.
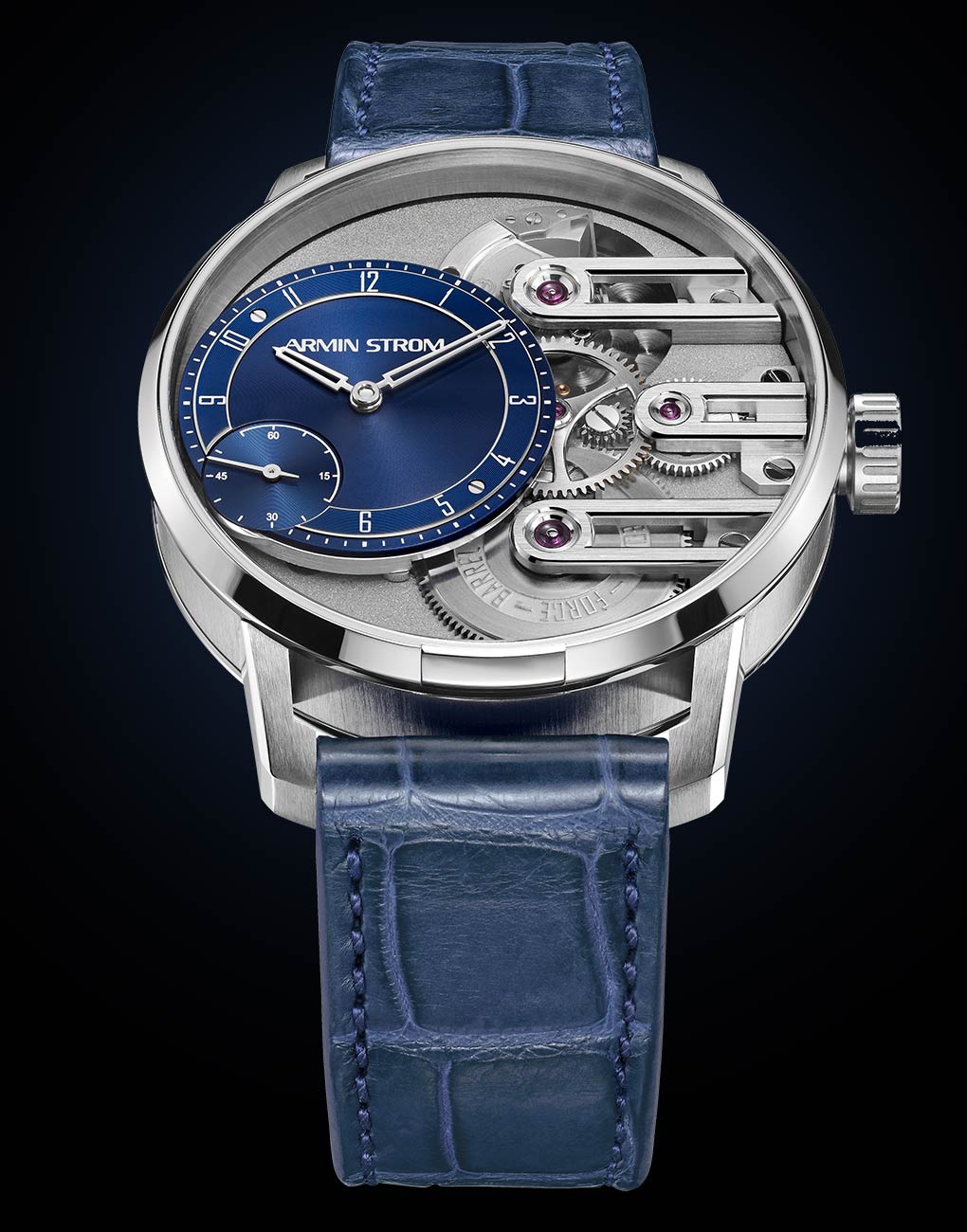
Armin Strom: The Genesis And Evolution
Established in 1967 by master watchmaker and eponymous horologist, the first Armin Strom workshop was set up in Burgdorf, Switzerland. Apart from watchmaking, Armin Strom also offered restoration services. Gradually, the company developed an unparalleled skill set in the art of hand-skeletonisation—which continues to grace its watches even today. In fact in 1990, Armin Strom earned a Guinness World Record after the brand created the world’s smallest hand-skeletonised watch for ladies. However, in 2006, the baton was passed on to watchmaker Claude Greisler and entrepreneur Serge Michel—childhood friends, who together revitalised the brand with the opening of Armin’s Strom’s first fully-integrated manufacture in 2009. And the following year, they presented the One Week Collection with the ARM09 hand-wound movement at Baselworld, which introduced a new watchmaking chapter for the brand.
Both Greisler and Michel have always considered the movement as the heart of a watch, hence they felt it was essential to become a manufacture, producing their own movements. As Greisler explains, “This was not just a question of designing our own movements. It allowed us to select the best brass and steel in order to make the best possible plates, bridges, screws and pinions. Moreover, we wanted to do the electroplating, finishing and assembly in-house, providing us greater control and independence.”
Today the brand designs, develops, mills, embosses, galvanises, hand-finishes and assembles all its watches in-house; bringing even the most complicated ideas to life without any of the compromises that typically stem from reliance on a supply chain. The company is headquartered at Biel/Bienne, Switzerland and it is here that the brand churns out timepieces that offer a unique fusion of the Swiss-German horological tradition, driven by an unwavering commitment to innovation—all while having a firm control on volume production. These timekeepers stand out for their ‘exposed’ dial-side movement mechanics, which the brand also calls ‘transparent mechanics’, where every part is hand-finished to the highest haute horlogerie standards.
“Armin Strom represents a unique fusion of the Swiss-German horological tradition, avant-garde ‘transparent mechanics’ and an unwavering commitment to horological innovation,” says Serge Michel, the driving business force behind the brand. He also points out that Armin Strom firmly believe that horological craftsmanship should never be hidden behind a dial. That’s why each time you check the time on an Armin Strom watch, you will also rediscover the movement’s depth. The brand is also firmly guided by the quest for constant innovation, and are always rethinking watchmaking ideas. This lies at the core of all their watches that reveal the function, beauty and sophistication of moving mechanics, where one can admire the timepieces in all their glory.
The Modern-Day Armin Strom: A Fully-Integrated Manufacture
Since 2009, the manufacture has developed 13 exclusive calibres and produces all of its timepieces in-house. A team of dedicated engineers and artisans, led by master watchmaker and co-founder Claude Greisler, uphold that tradition with uncompromising commitment. “A passion for ‘transparent mechanics’, both from an aesthetic perspective and to showcase how our watches actually work, has always guided my design sensibility. From a watchmaking perspective, I honour the many generations of Swiss-German watchmakers in my family with an uncompromising commitment to perfection in both movement quality and finishing,” states Greisler.
While Armin Strom are a vertically integrated complete horological manufacture, every movement is the brainchild of Claude Greisler. He conceived the revolutionary Mirrored Force Resonance movement, sketching his ideas on paper before they were input into a CAD system (computer-aided design) and the process of modelling the movement began. Like so many things at Armin Strom, all of this is done in-house, with the dimensions calculated down to a precision of one micron. This essential data instructs the various machines on how to make numerous movement components—majority of which, with the exception of the escapement and the balance spring, are produced in-house. Small round components like screws, pinions and gear wheels are produced using profile-turning machines. Long steel or brass rods are cut from the side to form teeth or axles. Larger components, such as base plates and bridges, are produced from brass using CNC (computer numerical control) machines. These are capable of machining along multiple axes following a programmable sequence. This involves using different tools for different operations and moving the component with robotic arms.
Particularly small and delicate components, such as small bridges, levers and springs, are produced using wire erosion. This involves threading a wire that is not much smaller than a human hair through a tiny hole in the metal. The working plate is immersed in a dielectric liquid. An electrical current passes through the wire which react with the dielectric liquid, thereby eroding minuscule amounts of the metal. This process allows particularly delicate operations to be performed while maintaining the structural integrity of the metal. Incidentally, Armin Strom does not produce any of its components by stamping because of the stresses that this places upon the metal.
Once the raw components are manufactured, they are engraved, bevelled, polished and decorated. Circular graining and Geneva stripes are applied by hand before the components are passed to the in-house electroplating department. Initially, steel and brass components are subjected to gold plating before a layer of nickel is added to prevent corrosion and harden the surface. These are then passed on to master watchmakers for movement assembly. The jewels are then set within the baseplate and bridges, after which the gear train and mainspring are added. And the movement comes alive once the escapement and balance wheel have been fitted, before being completely disassembled. The various parts are cleaned and dried before being re-assembled and lubricated. Finally, after several days of testing, the watch is ready for dispatch.
In Focus: Watches At A Glance
Today the brand are focused on two major collections—System 78 and Resonance—which are doing very well for them on the market. Armin Strom are one of the few players in the watchmaking business to manufacture series-produced resonance watches. This milestone was achieved in 2016 with the introduction of the Mirrored Force Resonance—a game-changing resonating dual regulator developed for maximum chronometric precision, with a captivating oscillation mechanism on the dial-side of the watch.
In a resonance watch, two balance wheels (oscillators) must regulate each other’s oscillation frequency so as to render the watch immune to the disruptions caused by the unpredictable motion of the human wrist. The challenge was to consistently maintain the resonance state, and to thereby maximise its chronometric benefit—a feat that no other resonance watch has been able to replicate till date.
The System 78 collection was conceived in 2020 to offer fine watchmaking, impeccable finishing and a number of innovative horological ‘firsts’ while maintaining an accessible entry-level price point. The collection embodies the watchmaking sensibilities of Claude Greisler and Serge Michel, who were both born in 1978. The notable series that form a part of this collection are: Tribute 1, Lady Beat and Gravity Equal Force (GEF)—a perfect representation of the System 78 philosophy. While the Tribute 1 is a modern reinterpretation of the dress watch that’s both technically superior and beautifully hand-finished; the Gravity Equal Force is the world’s first automatic watch with constant force transmission, achieved by combining a stop-work declutch mechanism with an automatic winding movement, supplying consistent power transmission, thereby resulting in impeccable precision and accuracy.
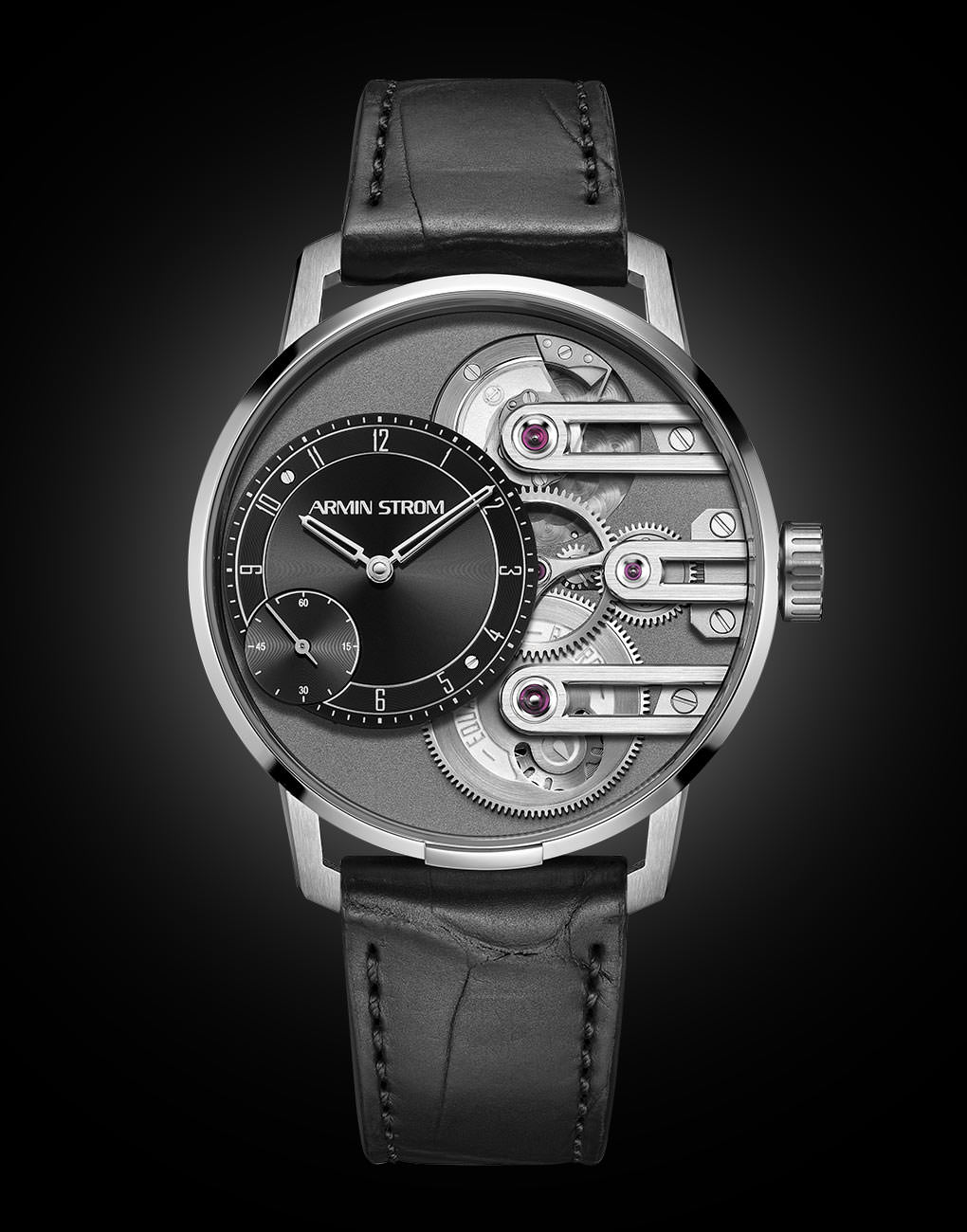
As a young independent, Armin Strom are charting their own course in the haute horlogerie universe, and have managed to establish a unique identity for themselves with their avant-garde watches that allow one to get a glimpse into what’s making them tick. Not to be confused with the usual ‘open-worked’ timepieces; these masterpieces fuse the movement and dial seamlessly to offer a complex yet beautiful time-telling display for each creation.
