FeatureGrab Your Coat: The Ultimate Guide To Understanding Metal Coating And Treatment On Watches
Since the 1840s, watchmakers have been coating timepieces in a bid to elevate their looks and durability. Here’s a look at some of the most prominent types of coatings used in the industry and what makes them so popular
May We Recommend
Choosing the perfect timepiece is by no means a cakewalk. From keeping in mind the capability of a movement to selecting the material of the watch; from pondering over the brand and their history to making sure that the watch is comfortable to wear, there are many factors to consider before one decides to shell out a small fortune on an exquisite piece of timekeeper. Often a part of these considerations is the coating of a watch. Its purpose is two-fold. It not only contributes to the overall aesthetic of the timekeeper, but also enhances the durability of the watch by shielding it from everyday wear and tear. Therefore, it’s not surprising that watch manufacturers have been coating their timepieces for more than one and a half centuries now. Over the years, the horological industry has witnessed a variety of coatings and treatment methods but the most notable ones include electroplating, PVD coatings and DLC coating. So, let’s delve a little deeper and try to understand what they actually mean and how these coatings became a mainstay in the industry.

Electroplating: The Oldest Way Of Coating
The earliest signs of coating timepieces can be found during the 1840s when watch manufacturers began to use electroplating for applying gold on watch cases. The process involves immersing the parts to be coated in a chemical solution containing the covering metal. Then, electricity is passed through this solution and by the process of electrolysis, the suspended molecules of gold are transferred to the surface of the components needed to be coated. Electroplating became so popular over time, especially during the early 20th century, that some watchmakers, such as Chopard, established in-house electroplating departments in order to protect treated components from oxidising or getting scratched during transportation. However, this process came with some major drawbacks.
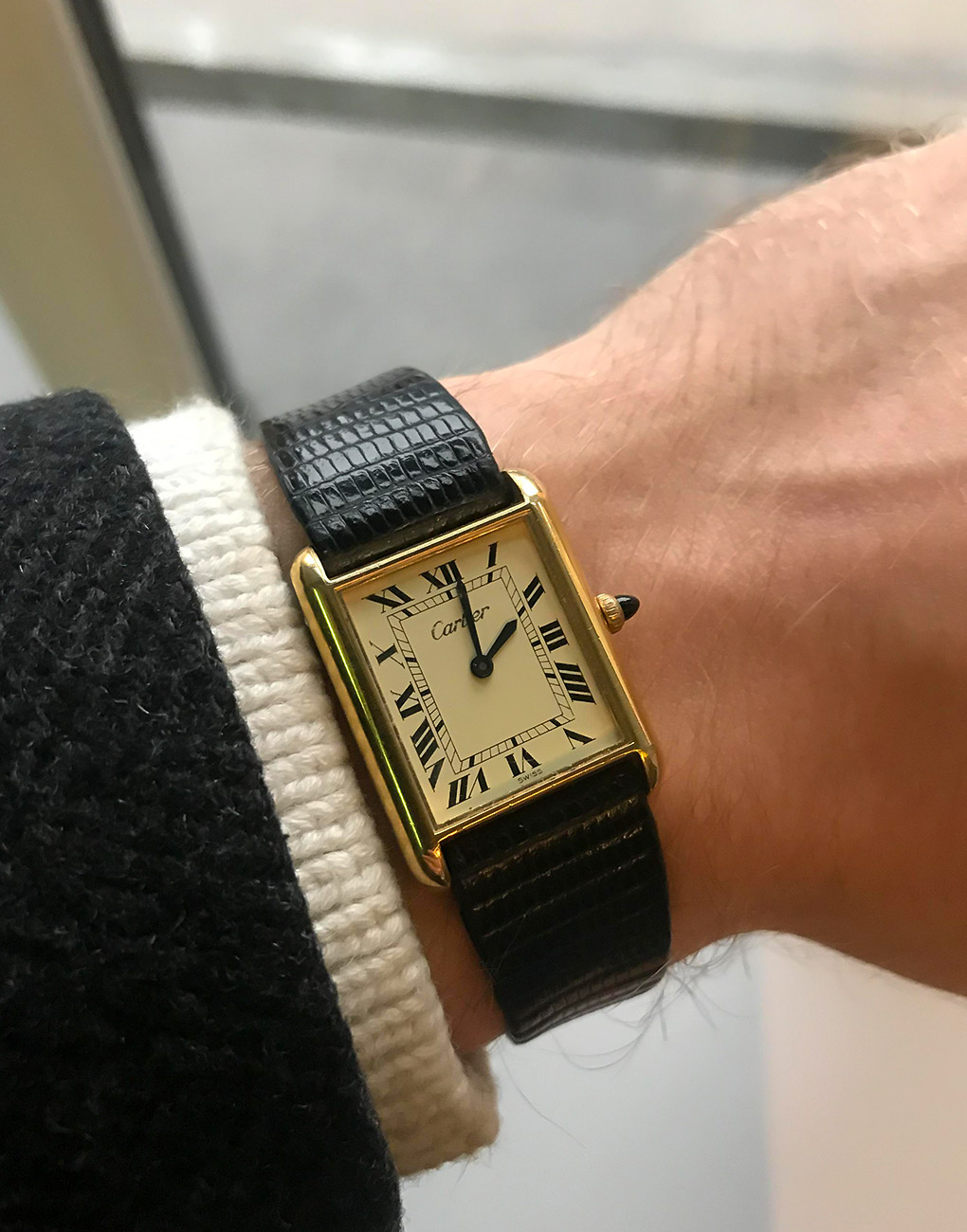
One of the major issues with electroplating is that due to the remarkably layer of the coating—usually sized at just two micrometres—the watch cases were highly susceptible to scratches. Another flaw was that the coating tended to cause allergic reactions to the skin, which could be really unpleasant and irritating. As a result, watchmakers eventually began to phase out electroplating for most parts and replaced it with the physical vapour deposition (PVD) coating process.
PVD Coating: The Modern Treatment
PVD is quite an old process of metal plating and its roots can be traced back to 1838 when English scientist Micheal Faraday first used it during his experiments with electricity. Part of the reason for its widespread popularity is that it’s not only long-lasting but also completely eco-friendly. Speaking in the simplest terms, the PVD coating process refers to the application of an extremely thin layer of material onto the surface of components that need to be protected from corrosion and other kinds of damage. The most common coating materials are titanium, aluminium, and gold. And these coatings can be applied to a wide variety of substrates—the base on which the coating is done—including stainless steel and ceramic.
The process is carried out in a vacuum chamber at a temperature between 50 and 600 degrees Celsius, where the components that need to be coated are kept, and a negative charge is placed on them. After this, the material that is to be used as a coating is heated to transform into vapours and then a positive charge is placed through them. Simultaneously, a reactive gas such as nitrogen is introduced in the same vacuum chamber where it chemically reacts with the previously evaporated material to form the PVD coating, which sticks to the components to be coated—just like opposite poles of two magnets attract each other.

Despite being available for the longest time, PVD-coating was used on timepieces only in 1972 with the launch of Porsche Design Chronograph 1—the first all-black watch that took advantage of this process and exuded a compellingly serious, masculine vibe. Then, three years later, TAG Heuer (then known as Heuer) released their well-known square-shaped Monaco with a matt PVD case and brought the process to the centre stage. Thanks to its mesmerising looks and forward-looking technology, the Heuer ‘Dark Lord’ Edition garnered huge fanfare and became one of the most coveted timepieces of its generation.

Since then, almost every high-end watch manufacturer have used PVD to elevate the looks and resilience of their timepieces. Although, over the years, this type of coating has evolved and become much more resistant to environmental factors such as scratches, oxidation or temperature changes, it isn’t permanent, unfortunately, and begins to wear off over time. This led the watchmakers to further push the boundaries of innovation and look for better alternatives such as the coating of diamond-like carbon (DLC).
DLC Coating: The New And Improved Treatment
In modern watchmaking, DLC coating enjoys a cult status. Often mistaken as a synonym of PVD, it’s a type of coating which is done through the PVD coating process and not a process itself. As its name suggests, DLC coating uses carbon to achieve a diamond-like layer. Thinner than human hair, it is stronger than raw steel and can reach a hardness of up to 9,000HV (Vickers). In comparison, plaster of paris, which gets very easily scratched has a hardness of 36HV, whereas, diamond offers a hardness of 10,060HV. Not only this, owing to its diamond-like properties, DLC coating is bound to stay put and doesn’t wear off anywhere as quickly as other conventional PVD-type coatings. Some experts suggest that DLC-coating can increase the life expectancy of a surface by a whopping 85 years.
Apart from its physical attributes, DLC coating makes for a visual treat too. With its colours ranging from anthracite to deep black, this type of coating perfectly imparts a uniform and stealthy aesthetic to the timepiece and is an ideal choice for those who dig all-black watches. Owing to the aforementioned benefits and properties, DLC coating has been widely used on dive watches and other kinds of sports and military watches that are crafted to endure harsh outside conditions.
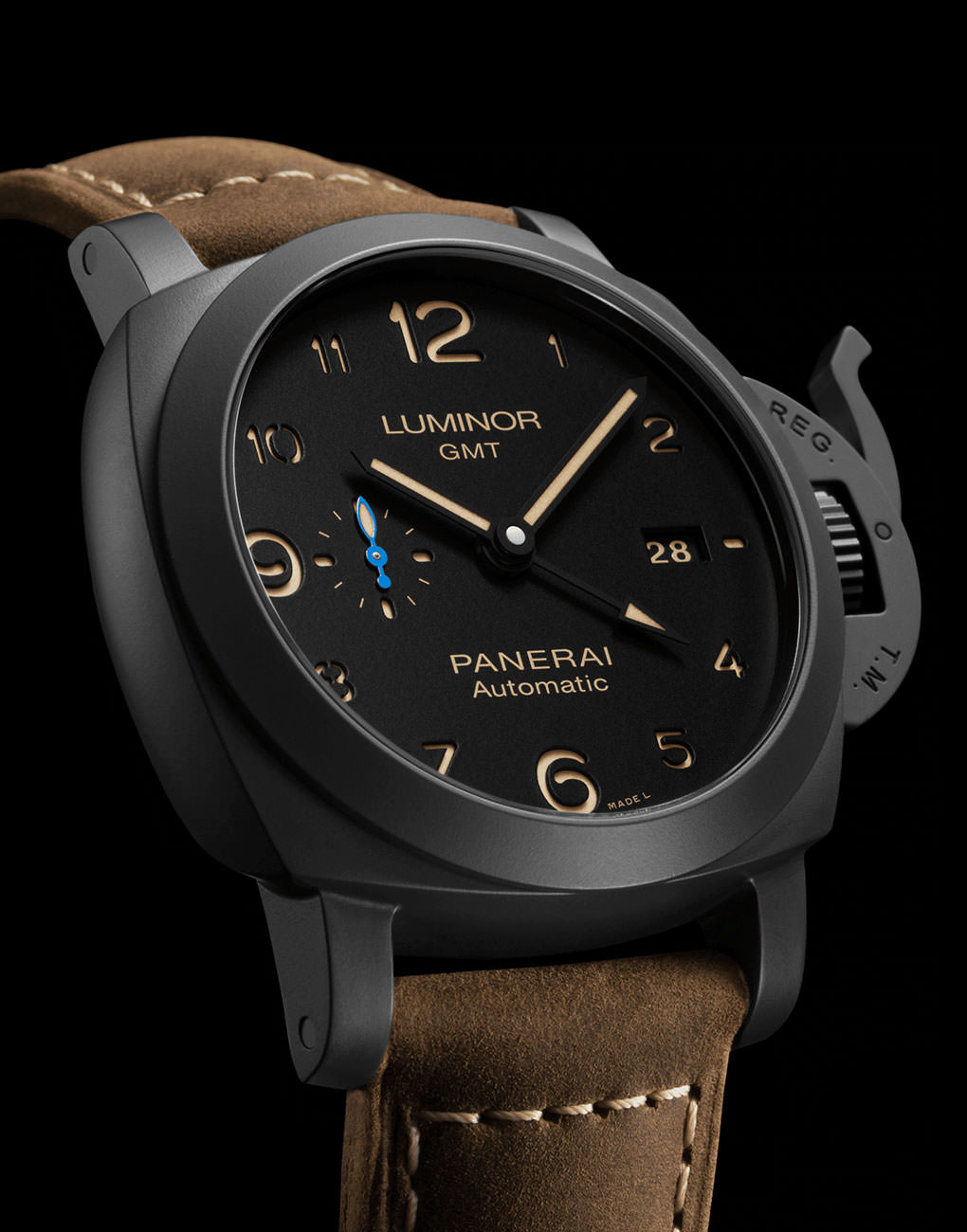